Pulsed Laser Deposition System
PLD System, PLD-Rheed System, UHV PLD-Rheed System, Wafer Scale PLD System
TSST, Twente Solid State Technology, The Netherlands
PLD SYSTEM
TSST Pulsed Laser Deposition systems for thin film growth are state-of-the-art, highly flexible systems for thin film research at atomic level, ideally suited and field proven for research on a large variety of materials including complex oxides.
Our customised design approach allows various types of heating, with which temperatures up to 1000°C are obtained. A base pressure below 10-7 mbar is guaranteed, with UHV upgrade possibilities. Pressure is regulated through automated upstream and downstream control, which combines fast pressure set-point control.
To guarantee high vacuum quality, the system can be equipped with a load-lock for sample and target carrousel exchange, optionally extended with heater and target storage possibilities. A six targets carousel is mounted on a stage which is controlled by the software, including spinning of the targets to ensure a large ablation area and prevent drilling.
A short outline:
- Thin film growth of highest quality complex materials
- Fully customised design, including adaptation to a specific lab layout
- Remote support, service and on-site training by TSST engineers
- Down to 10-7 mbar base pressure
- Up to 1000°C growth temperature
- Up to 6 different targets for heterostructure growth.
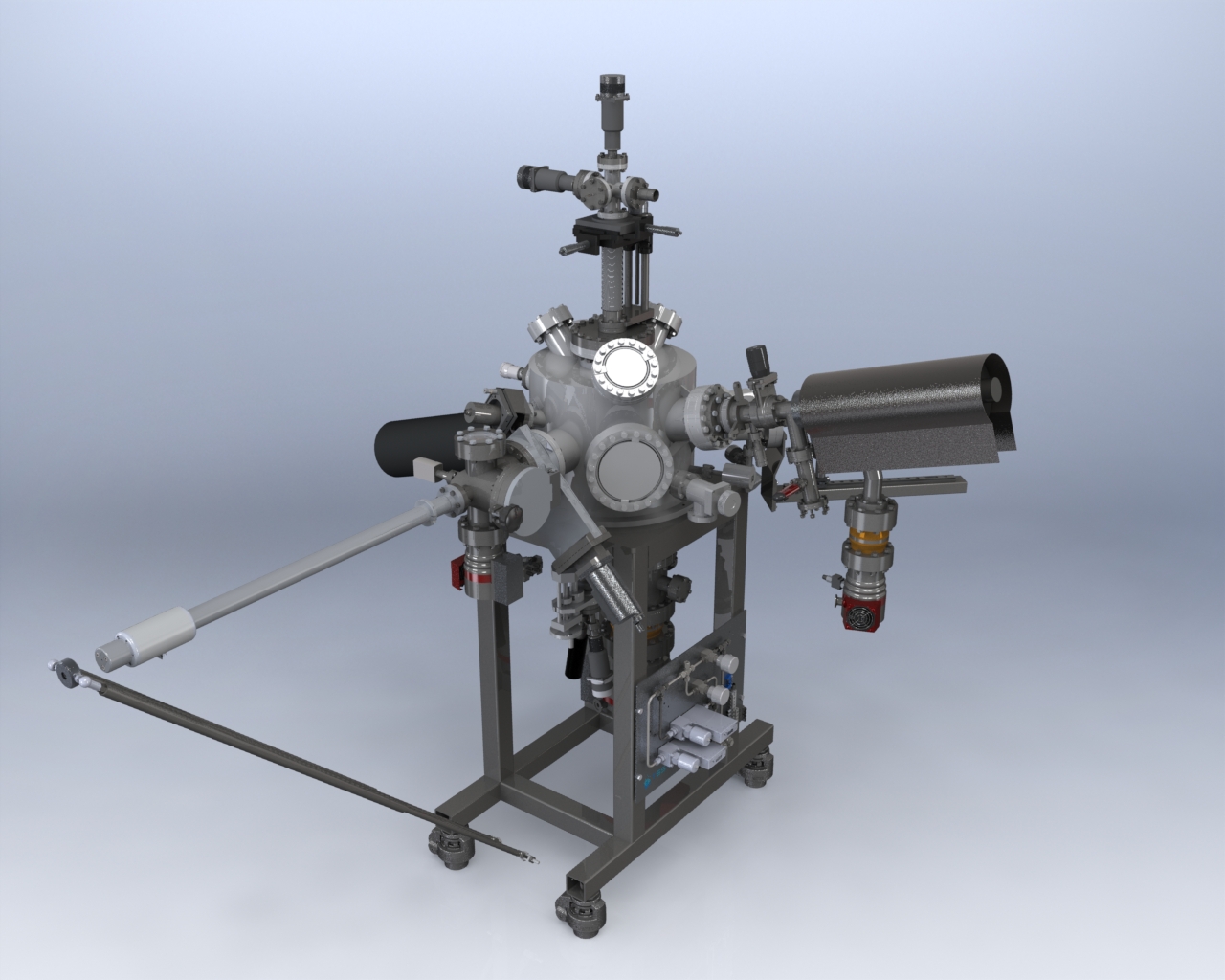
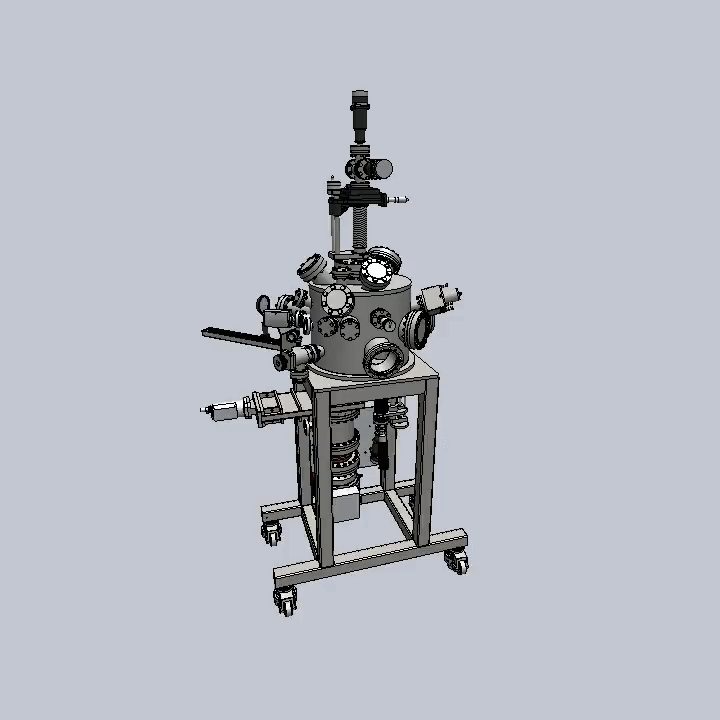
PLD-RHEED SYSTEM
TSST Advanced Pulsed Laser Deposition systems with in situ RHEED are state-of-the-art, highly flexible systems for thin film research at atomic level, ideally suited and field proven for research on a large variety of materials including complex oxides.
With the presence of high pressure RHEED in our advanced PLD system configuration, single monolayer growth can be monitored and controlled at standard process pressures. To obtain maximum possibilities for extensive sample surface electron diffraction studies, the heater stage is designed with all necessary degrees of freedom for optimal alignment.
Our customised design approach allows various types of heating including laser heating, with which temperatures up to 1100°C are obtained. A base pressure below 10-8 mbar is guaranteed, with UHV upgrade possibilities. Pressure is regulated through automated upstream and downstream control, which combines fast pressure set-point control with vibration limiting conditions for optimal RHEED growth monitoring.
To guarantee high vacuum quality, the system is equipped with a load-lock for sample and target carrousel loading, optionally extended with heater and target storage possibilities. A six targets carousel is mounted on a scanning stage which is controlled by the software. Various scanning patterns can be programmed, which makes it possible to use irregular shaped targets.
A short outline:
- Thin film growth of highest quality complex materials
- Single monolayer growth control with RHEED
- Fully customised design, including adaptation to a specific lab layout
- Remote support, service and on site training by TSST engineers
- Down to 5.0 x 10-9 mbar base pressure
- Up to 1100°C growth temperature
- Up to 6 odd shaped targets for heterostructure growth
UHV PLD-RHEED SYSTEM
TSST Advanced Pulsed Laser Deposition systems with in situ RHEED are state-of-the-art, highly flexible systems for thin film research at atomic level, ideally suited and field proven for research on a large variety of materials including complex oxides.
With the presence of high pressure RHEED in our advanced PLD system configuration, single monolayer growth can be monitored and controlled at standard process pressures. To obtain maximum possibilities for extensive sample surface electron diffraction studies, the heater stage is designed with all necessary degrees of freedom for optimal alignment.
Our customised design approach allows various types of heating including laser heating, with which temperatures up to 1100°C are obtained. A base pressure below 10-8 mbar is guaranteed, with UHV upgrade possibilities. Pressure is regulated through automated upstream and downstream control, which combines fast pressure set-point control with vibration limiting conditions for optimal RHEED growth monitoring.
To guarantee high vacuum quality, the system is equipped with a load-lock for sample and target carrousel loading, optionally extended with heater and target storage possibilities. A six targets carousel is mounted on a scanning stage which is controlled by the software. Various scanning patterns can be programmed, which makes it possible to use irregular shaped targets.
A short outline:
- Thin film growth of highest quality complex materials
- Single monolayer growth control with RHEED
- Fully customised design, including adaptation to a specific lab layout
- Remote support, service and on site training by TSST engineers
- Down to 5.0 x 10-10 mbar base pressure
- Up to 1100°C growth temperature
- Up to 6 odd shaped targets for heterostructure growth
RHEED System
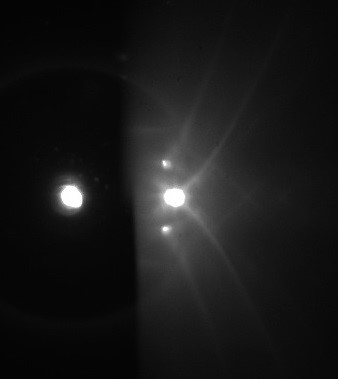
Reflection High-Energy Electron Diffraction (RHEED) has proven to be a very versatile technique for growth and surface studies of thin films. The combination of the forward scattering geometry of RHEED with the arrangement of pulsed laser deposition, in which the plasma plume is incident normally on the substrate, enables diffraction features to be monitored during growth. In RHEED, high-energy electrons with energies of 10-35 kV are incident on the surface of a crystal at a grazing angle of a few degrees (1-5°). The high-energy electrons only interact strongly with the first few layers of a material, because of the grazing angle. This makes RHEED extremely sensitive to surface morphology, with which it is possible to investigate the surface structure and morphology in-situ and real time during growth.
Monolayer growth control
RHEED can be used for the structural analysis of crystal surfaces and the investigation of the growth kinetics of thin films by monitoring the variations in the intensity of various features in the RHEED pattern. It has been shown that during growth, the intensity of RHEED patterns (during experiments typically the intensity of the main specular spot is tracked) show an oscillatory behaviour, which directly relates to the growth rate. The oscillations are associated with periodic changes in the roughness of the growing surface, as atoms forming a new monolayer gradually fill vacant surface lattice sites.
Specification
RESEARCH –RHEED
- The system includes a 30keV RHEED-gun to which an differentially pumped extension tube is connected with a pinhole close to the substrate. This design, developed at the University of Twente, makes it possible to carry out RHEED measurements at higher pressures, typically necessary for high crystalline growth of oxide materials. The entire RHEED-gun and extension can be mounted on an XY-stage to allow for electron beam adjustment with respect to the substrate. A valve can be included to isolate the RHEED gun from the chamber to allow atmospheric pressure annealing.
- Opposite to the electron gun a phosphor screen is mounted on a flange that extends into the chamber to position the screen as close as possible to the substrate. A metal shield is attached to the phosphor screen to avoid contamination. Data acquisition for the software is realised with a camera capturing the image on the screen. An optional shutter can be mounted to protect the phosphor screen during depositions without RHEED.
Wafer Scale PLD System
하기