The HEX Series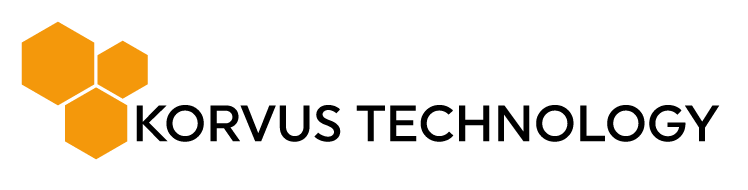
Modular PVD Systems
HEX 시리즈는 독창적인 모듈식 아키텍처를 갖춘 벤치탑 장비로서, 박막 증착 분야에 비교할 수 없는 수준의 사용자 제어, 커스터마이즈 및 업그레이드가 가능합니다.
HEX 플랫폼은 최신 박막 기술과 성능을 도입한 벤치탑 PVD 시스템입니다.
기존 PVD 챔버와 달리 HEX의 오픈 프레임 아키텍처를 통해 사용자가 기기를 자유롭게 재구성하거나 업그레이드할 수 있으며, 다양한 옵션의 추가가 가능합니다. 따라서 증착 연구 시 어떤 방향으로 진행되더라도 본 시스템을 통해 원하는 목표를 달성할 수 있습니다.
Concept
컴팩트하고 매우 유연한 박막 증착 시스템.
Design
HEX 시리즈 디자인의 모듈식 특성은 전문적인 도구가 없어도 패널을 몇 분 만에 프레임에 장착할 수 있음을 의미합니다.
Trusted by 100+ world-class brands and organisations of all sizes
The HEX Series
Thin Film Deposition
-
Thin Film Deposition System - HEX and HEX-L
-
HEX-L Cluster System
-
Thin Film Deposition Deposition Sources for HEX sereis
-
Sample stages for HEX sereis
-
Thin Film Deposition Components and Software for HEX sereis
-
HEX Sereis Glovebox Integration
-
Compact Thin Film Deposition Equipment
HEX 시리즈 박막 증착 시스템은 증착 연구 애플리케이션을 위한 다양한 옵션을 제공합니다. 예산이나 용도에 따라 간단한 구성으로 기본 모델을 구입하고, 필요에 따라 더 높은 수준의 구성으로 업그레이드할 수 있습니다. 이러한 업그레이드는 모듈식이며 설치가 간단하므로 시스템의 가동중지 시간과 설치 비용이 줄어듭니다.
HEX 모델은 최대 8 × 10-7 mbar의 기본 진공과, 최대 100 mm의 샘플 크기를 수용하는 80 l/s 진공펌프가 함께 제공됩니다. 또한 시스템에는 여러 개의 작은 샘플을 동시에 수용할 수 있는 멀티 샘플 홀더가 함께 제공됩니다.
또한 본 시스템에는 4 × 10-7 mbar의 기본 진공을 달성하는 300 l/s 진공펌프를 포함하여 다양한 업그레이드 옵션이 포함되어 있습니다. 사용자는 최대 150 mm의 샘플 크기 또는 여러 개의 작은 샘플을 위한 공간이 있는 더 큰 HEX-L 챔버를 선택할 수도 있습니다.
Modular Design for Rapid Re-Configuration
HEX 시스템은 가벼우면서도 대부분의 물리적 증착 응용 분야에 충분히 견고한 6면의 알루미늄 프레임을 갖는 고진공 챔버로 구성됩니다. 육각형 구조는 다음을 포함하여 6개의 모듈식 패널을 지원합니다.
- Blank panel
- Viewport panel
- Deposition source panel
- Mass flow controller와 증착 두께 제어를 포함하는 PLD process control panel
- In-situ monitoring을 위한 QCM panel
이 디자인은 가스와 물 을 연결하기 위한 Hamlet quick connect과 샘플 스테이지 및 구성 요소 부착을 위한 개별 너트를 포함한 표준화된 피팅을 사용합니다. 이러한 표준화를 통해 간단하게 패널을 교체하고 시스템을 특정 어플리케이션에 맞게 조정할 수 있습니다. 또한 모듈식 설계로 인해 유지 관리 및 재구성이 더욱 빠르고 효율적으로 이루어집니다.
Custom Solutions for Your Requirements
당사는 증착 연구 고객의 어떠한 요구사항에도 고객사와 함께 가장 적합한 솔루션을 찾는데 협력하고 있습니다.
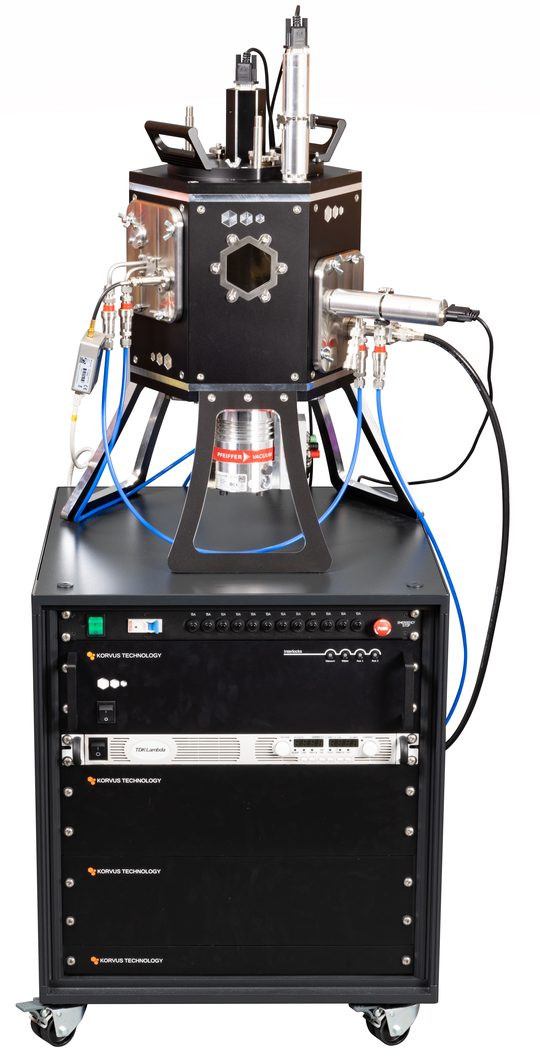
Designed With Research and Development in Mind
HEX 시스템은 모듈식 특성으로 인해 박막 증착 연구 개발에 이상적인 장비입니다. 모든 필수 요소에 접근성이 용이하여, 다양한 구성 요소를 테스트하고 다음을 포함한 여러 박막 증착 기술의 프로세스를 완벽하게 구현할 수 있습니다:
- 표면분석을 위한 샘플 전처리
- Sputtering
- Thermal evaporation
- 유기 PVD (Organic physical vapour deposition)
기본 모델에서 지원되는 method는 다음과 같습니다:
- 금속 및 포토레지스트 리프트-오프 공정
- EM 샘플 전처리
- 신규코팅 연구개발
- 마그네트론 스퍼터링 증착 최적화
사용 사례에 추가 기능이 필요한 경우 HEX 시스템에는 대부분의 박막 증착 프로세스에 대한 시스템 범위를 확장하는 다른 많은 모듈이 포함되어 있습니다.
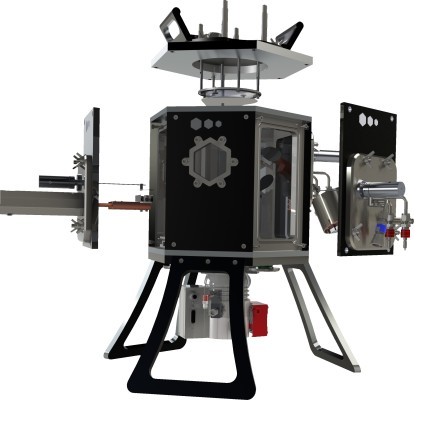
The HEX Series
Thin Film Deposition
-
Thin Film Deposition System - HEX and HEX-L
-
HEX-L Cluster System
-
Thin Film Deposition Deposition Sources for HEX sereis
-
Sample stages for HEX sereis
-
Thin Film Deposition Components and Software for HEX sereis
-
HEX Sereis Glovebox Integration
-
-
Applications
-
Publications
-
Webinars
The HEX Thin Film Deposition System Sources
HEX 시리즈는 다양한 증착 소스의 사용이 가능합니다. 이는 사용자의 용도에 따라 복합적으로 혹은 단일 소스만으로 구축될 수 있고, HEX와 HEX-L 모델 간에 전환이 가능합니다. 견고하게 설계되고 유지 관리가 용이한 Korvus Technology의 증착 소스는 HEX 및 HEX-L PVD 시스템에 이상적인 조합을 제공합니다.
TAU E-Beam Evaporation System
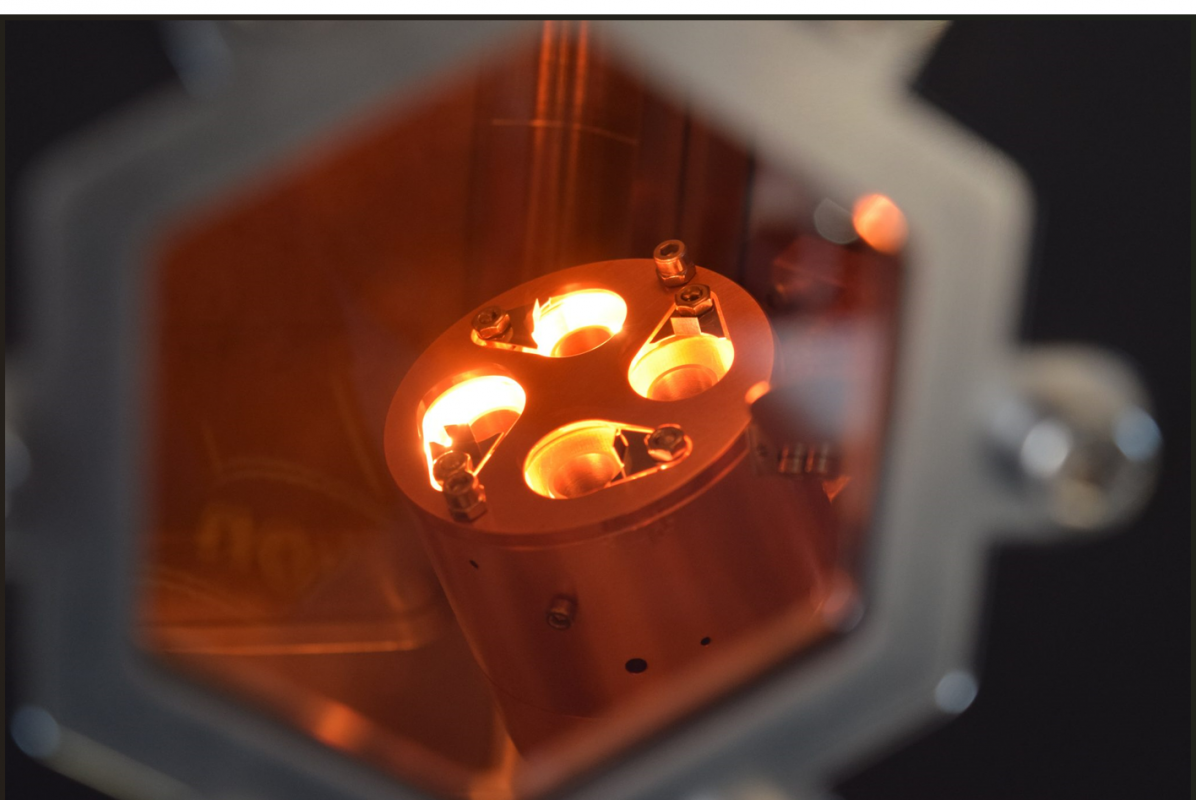
ORCA Organic Evaporation System
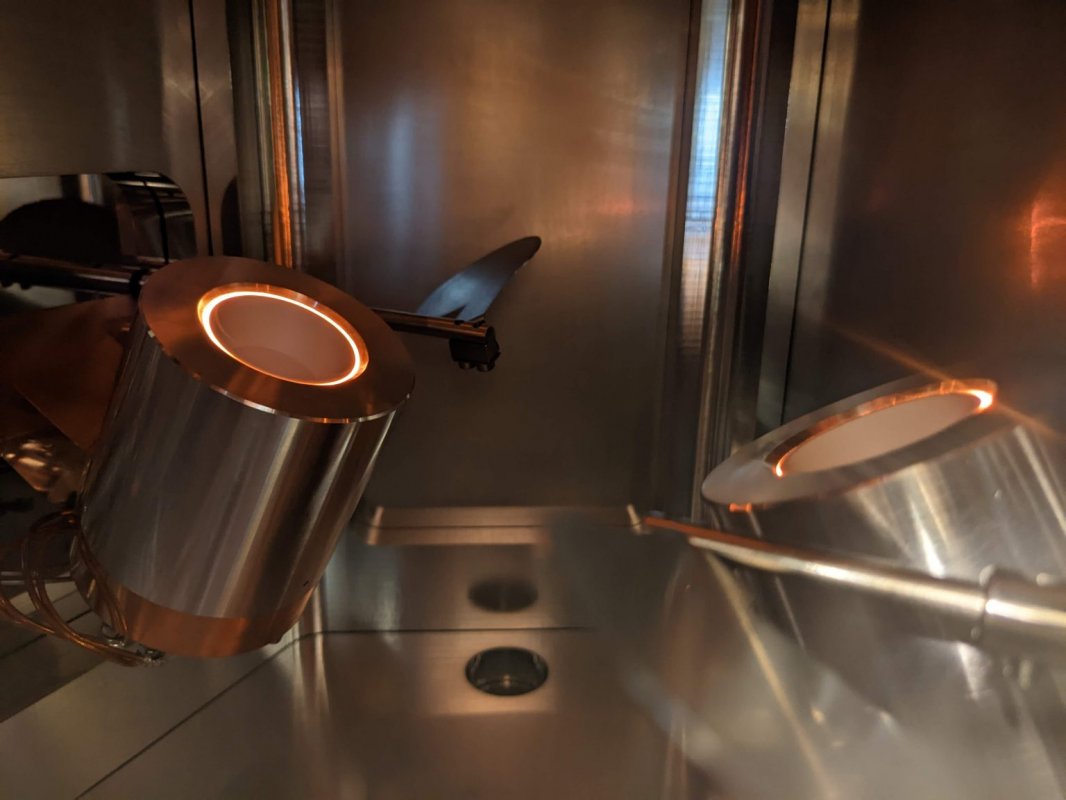
TES Thermal Evaporation System

Fission DC and RF Sputtering System
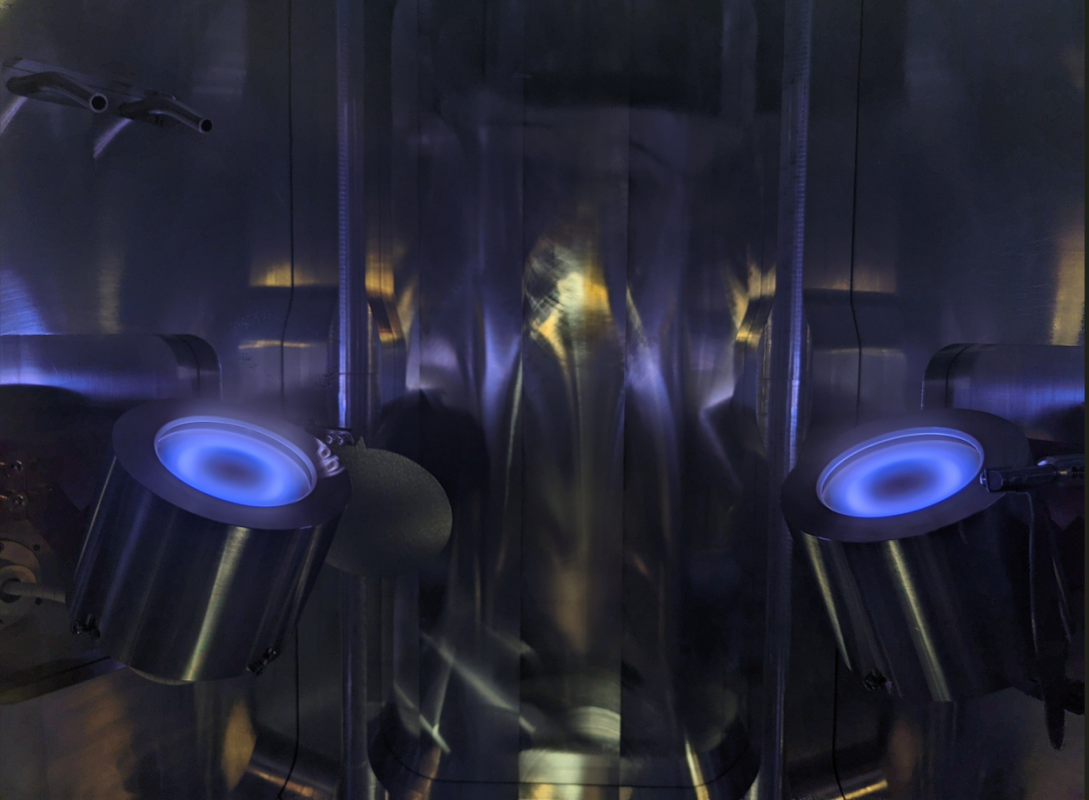
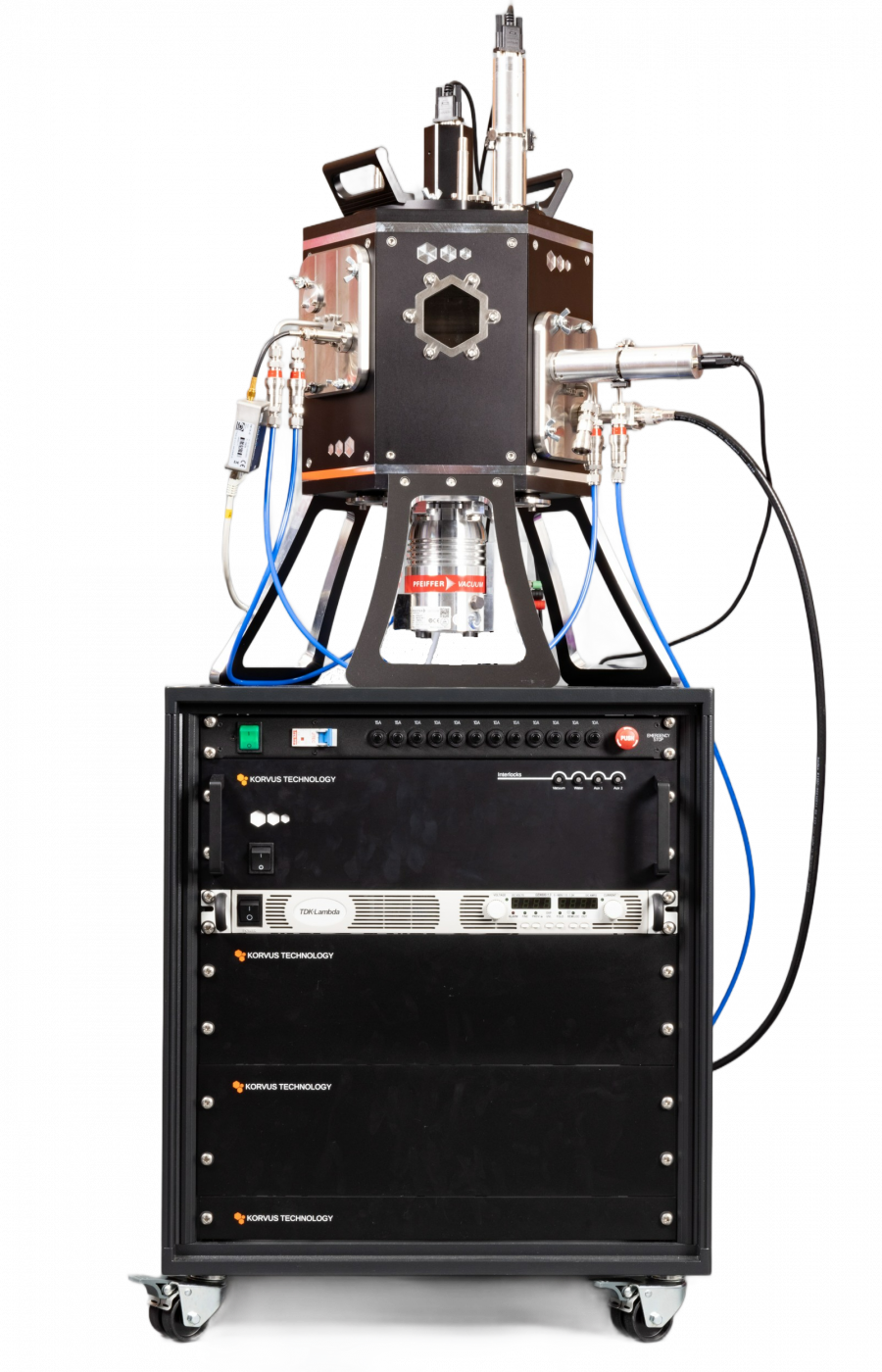
What Makes the HEX Series Unique?
Many bench-top thin film deposition systems are solid-state instruments that offer limited functionality. The HEX series is unique amongst thin film deposition systems due to its versatility — its modular design allows for customisation and robust user control features. Not only does this make the HEX ideal for teaching about various thin film techniques, but it also allows research and production facilities to incorporate the latest advancements in thin films into their bench-top system.
하기