For smarter and faster R&D and Production
SC-1 Series
(PE)-ALD and PVD without breaking the vacuum or move the samples between chambers to fabricate hundreds of multi-nanolayered films, reducing fabrication time!
SC-1 Series
⎯
The SC-1 is a ground-breaking and high-performing cluster equipment that combines Atomic Layer Deposition (ALD) with Physical Vapor Deposition (PVD) in an extremely compact, modular, and fully automated system for high-throughput production of multinanolayered coatings from the ALD and PVD materials library.
This innovative patent-pending cluster system revolutionizes the traditional cluster equipment, as it eliminates the need for transfer arms and multiple antechambers, which occupy a significant amount of lab space, with high acquisition, operating and maintenance costs.
・ Capable of performing both (PE)-ALD and PVD without breaking the vacuum or move the samples between chambers to fabricate hundreds of multinanolayered films, reducing fabrication time.
・ Scalable, modular and flexible system that allows to easily increase or decrease chamber dimensions, adapt new hardware and incorporate multiple in-situ metrology equipment.
The first (PE)-ALD and PVD cluster system in a compact and modular equipment
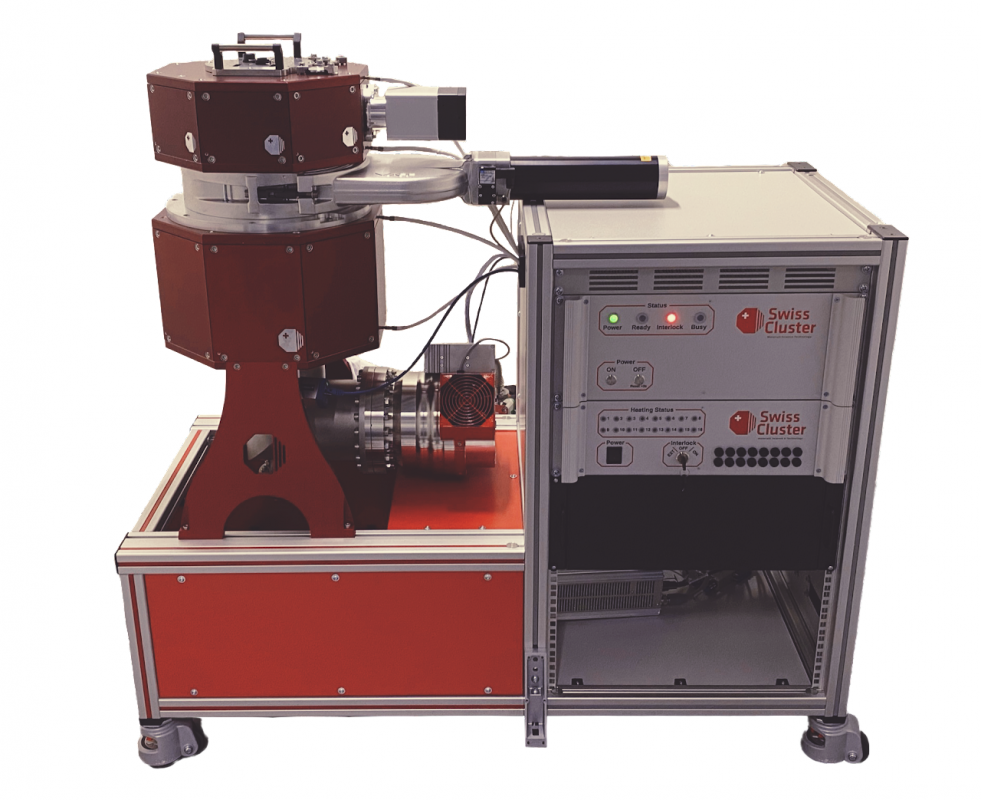
Why ALD and PVD?
The combination of ALD and PVD without breaking vacuum offer several advantages to fabricate advanced materials with tailored functionalities and properties. One of the primary benefits is the ability to achieve high-quality interfaces between the different layers of the coating material. The introduction of very conformal and pinhole-free films via ALD can stabilise the grain size of the PVD layers and hinder grain growth, which translates to improved mechanical and thermal properties.
Additionally, the material is not exposed to air and therefore there is no risk of contamination or oxidation. Since both ALD and PVD can deposit materials with atomic-level precision, combining the two techniques can allow for the creation of highly complex structures with unique properties that cannot be achieved using other methods.
Combining ALD and PVD without breaking vacuum can be a powerful approach to creating advanced materials with tailored functionalities and properties for a wide range of applications, including those in the semiconductor industry, optical coatings, hard coatings, and medical industry among others.
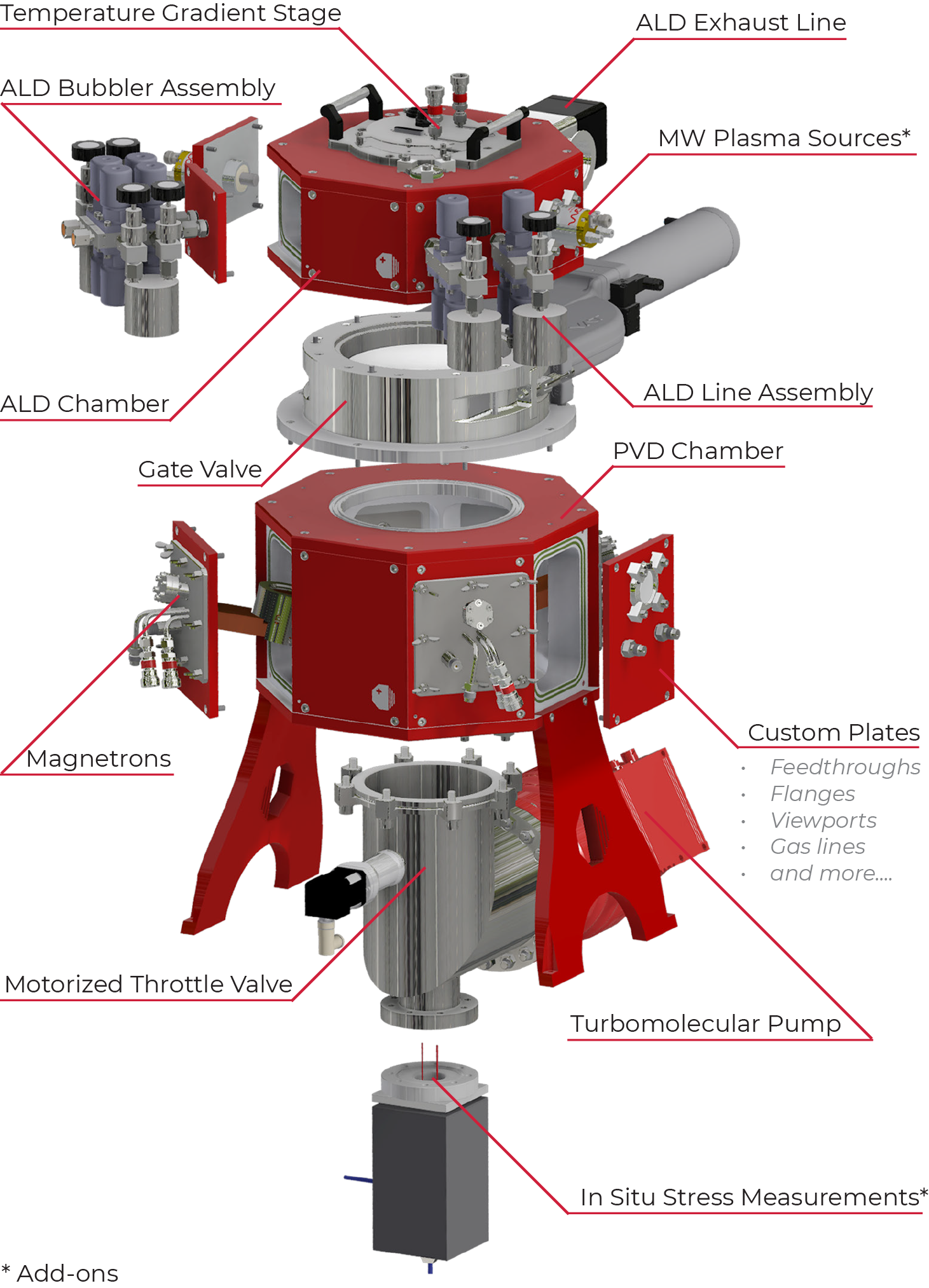
Technical Specifications
⎯
HARDWARE
Substrate Sizes
-
4 inch wafers
-
6 inch wafers
-
Different substrate holders available
Temperatures
-
Up to 400 °C
-
A gradient of 30 °C to 500 °C using our Temperature Gradient Stage
ALD Precursor Lines
-
Up to 12 precursors with individual inlets - bottles and bubblers
Magnetrons
-
Up to 4 magnetrons with 3 in. targets
Dimensions
-
L x W x H (1250 mm x 600 mm x 1210 mm)
Add-ons
-
Microwave plasma sources (PE-ALD)
-
In-situ wafer stress measurements
-
Customized ports and flanges
ALD-PVD Materials
-
Al2O3, TiO2, ZnO, Y2O3, ZrO2, HfO2, Cu, Al, Ti, and more...
ELECTRONICS & SOFTWARE
Mass Flow Controllers
-
4 Analog MFC
-
60 Digital MFC
Pneumatic (ALD) valves
-
24 valves
Pressure Sensors
-
4 Analog
Gate valves
-
3 gate valves with feedback
Flow meters
-
4 Flow meters
Temperature
-
16 Channel PID regulation with K-Type sensors
-
4 PT100/PT1000
Interlocks
-
8 Interlock in
-
12 Interlock out
Additional Connections
-
2 Ethernet
-
2 RS485
Building the Next Generation of
Thin Film Deposition System
Unique Systems / Smart Designs / Innovative Components / Combinatorial Deposition